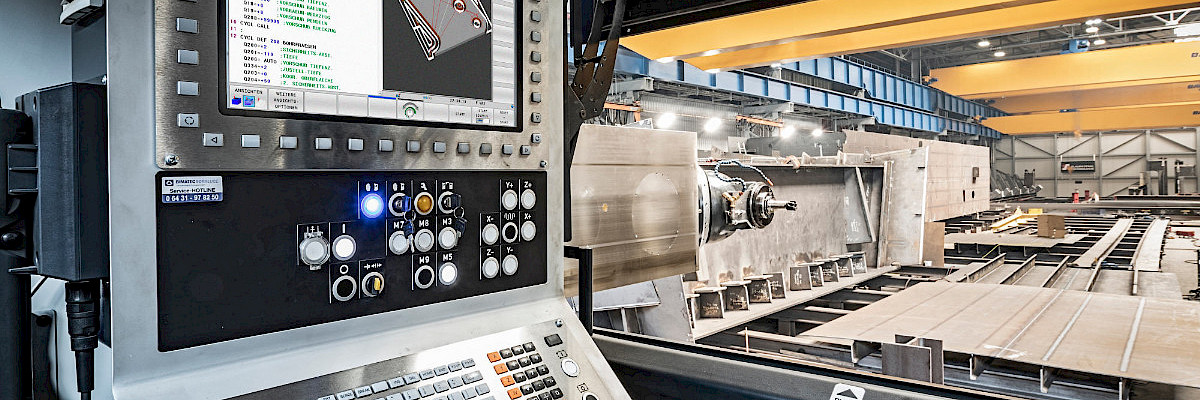
Digitale Innovation
Von der Konstruktion bis zur Montage:
Innovative digitale Technologien unterstützen unsere Prozesse und Maschinen.
Die Zukunft ist komplex.
Immer anspruchsvollere Konstruktionen gehen einher mit steigenden Anforderungen an
Effizienz, Qualität, Präzision.
Wir bei PST haben uns schon früh entschieden, nicht nur auf leistungsstarke Maschinen zu setzen – sondern auch auf innovative, digital gesteuerte Prozesse. Mit der Entscheidung für Aufbau einer digitalen Infrastruktur zur Produktionssteuerung und Produktionsbegleitung bewegen wir uns heute schon auf Augenhöhe mit den Herausforderungen der Zukunft.
Das Modell
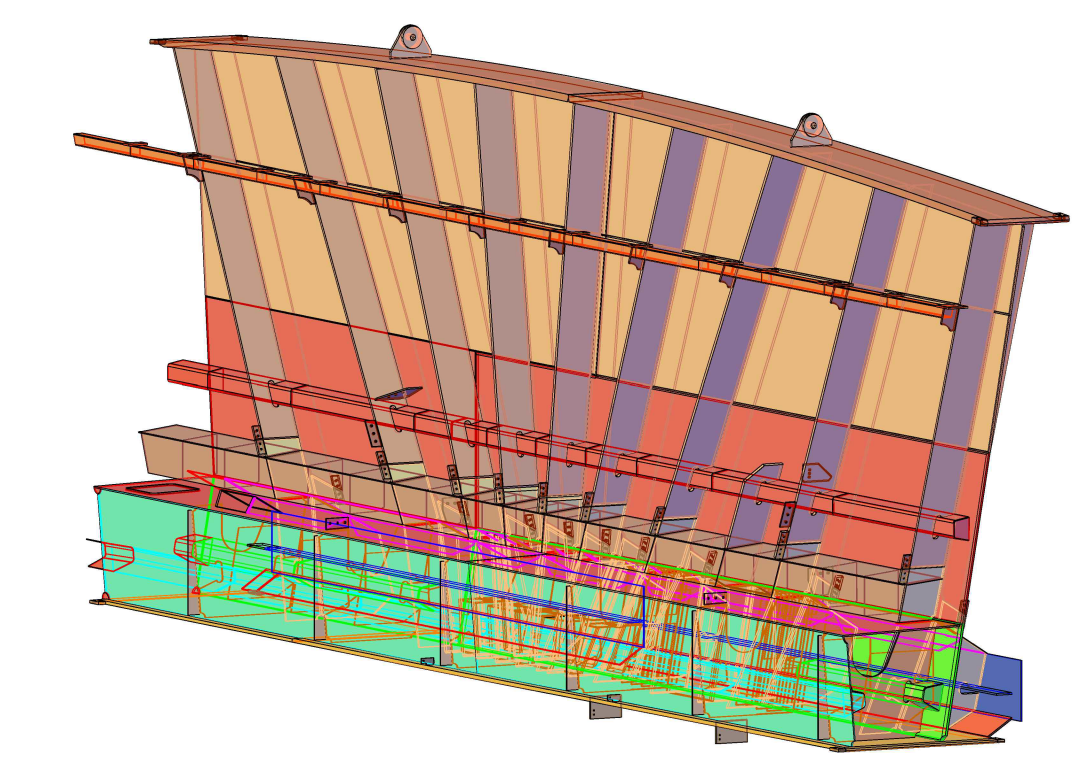
Bevor die Produktion überhaupt anläuft, entsteht in der Abteilung Konstruktion / Arbeitsvorbereitung ein sogenannter digitaler Zwilling. Der Zwilling wird die Produktion begleiten, bis das Bauteil fertiggestellt ist.
„Wir arbeiten mittlerweile in der Regel mit einem 3D-Modell“, erzählt Konstrukteur Frank Streit. „Das Modell wird im Rechner visualisiert. Sie können das Modell drehen, Koordinaten abgreifen, eine Kollisionsprüfung vornehmen. Aus dem 3D-Modell wird dann alles weitere abgeleitet: Zeichnungen natürlich, aber zum Beispiel auch Stücklisten für die Kalkulation oder den Einkauf.“
Das Modell erleichtert nicht nur die Erarbeitung aller notwendigen Unterlagen für unsere Abteilungen und den Kunden. Das Modell ermöglicht die Simulation und Prüfung aller produktionsrelevanten Aspekte. So erfolgt für alle Bauteile eine Kollisionsprüfung. Das Verformungsverhalten kann in der Konstruktion berücksichtigt werden. Produktionsbedingungen, logistische Einschränkungen oder Automatisierungsmöglichkeiten können früh im Projektverlauf festgelegt werden.
„Im Modell arbeiten wir im Maßstab 1:1. Eine Brücke, die in der Realität einen Kilometer lang ist, ist auch im Modell einen Kilometer lang. Wir können also an kleinste Details heranzoomen, können aber genauso auch das große Ganze in den Blick nehmen.“ (Jörg Neudel, Konstruktion / Arbeitsvorbereitung)
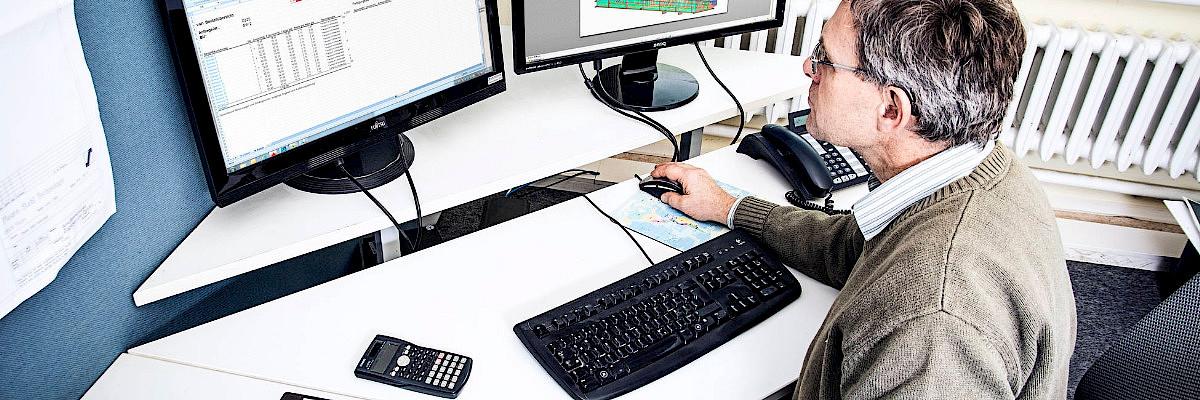
Planung und Einkauf

Wenn die Brücke konstruiert ist, werden die notwendigen Materialien mit den vorhandenen Gegebenheiten abgeglichen. Die so entstehende Auswertung bildet die Grundlage für die Fertigungsplanung und den Einkauf.
Welche Bleche in welcher Güte müssen bestellt werden? Welcher Aufwand für Zuschnitt und Bearbeitung muss kalkuliert werden? Welche Fertigungsfolge ist zu beachten – und wie verhält diese sich zu anderen, zeitgleich laufenden Projekten?
Die Bauteile
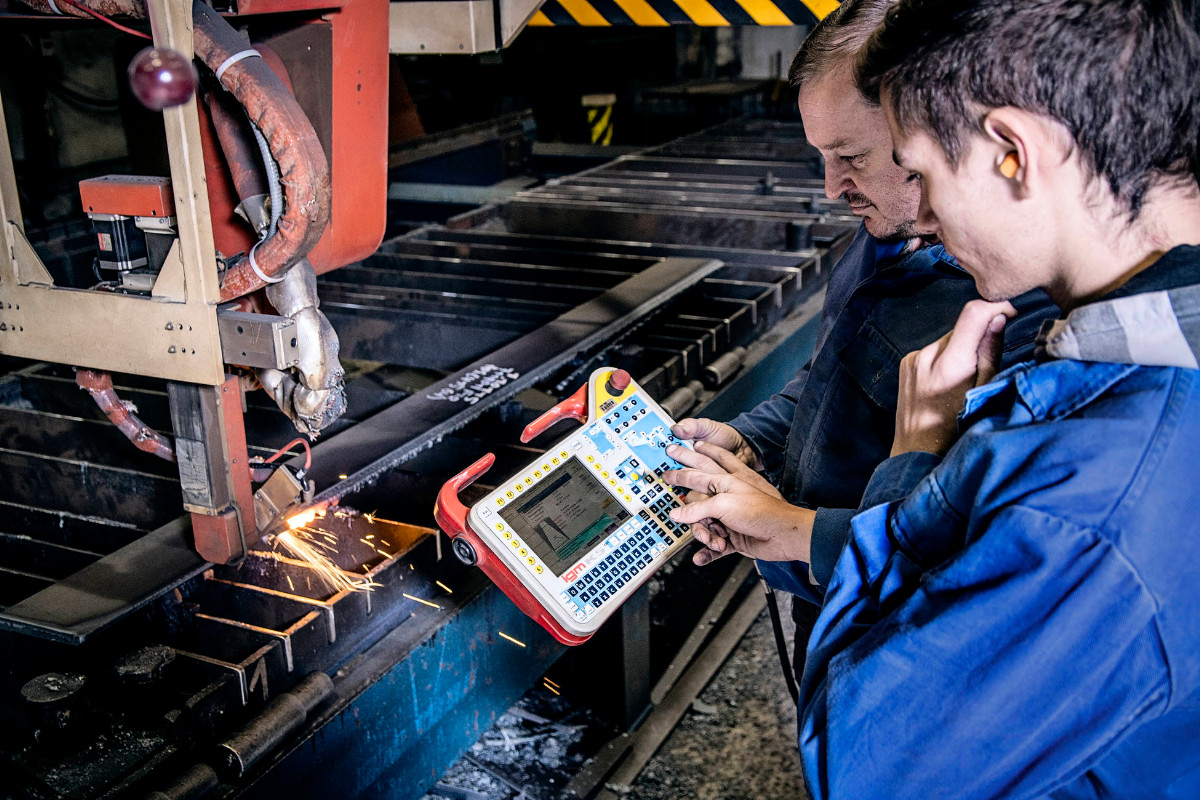
In der Arbeitsvorbereitung werden die einzelnen Bauteile aus dem Modell herausgelöst und als NC-Daten für den Zuschnitt aufbereitet. Dabei wird zwischen dem gewünschten Endzustand des Bauteils und dem Zwischenzustand in der Herstellung unterschieden, indem z.B. Fräszugaben oder Wärmezugaben berücksichtigt werden.
Die Datenübergabe erfolgt im DStV-Format. Dieser vom Deutschen Stahlbauverband entwickelte Standard definiert u.a. wie die Daten an die Maschinen in Zuschnitt und Fertigung zu übergeben sind.
Das Datenpaket für ein Bauteil enthält jedoch nicht nur geometrische Informationen zur Steuerung der Bearbeitung durch die Maschine; auch die Steuerung der Fertigungslinie erfolgt digital. So wird im Rahmen der Arbeitsvorbereitung definiert, welche Maschinen das Bauteil in welcher Reihenfolge durchlaufen soll.
„Auf Basis der Modelle können wir mit den Einzelteilen Zusatzinformationen wie Qualitätsmerkmale oder Stahlgüte übergeben. Das erleichtert die Arbeit und schafft Sicherheit.“ (Frank Streit)
Die Fertigung
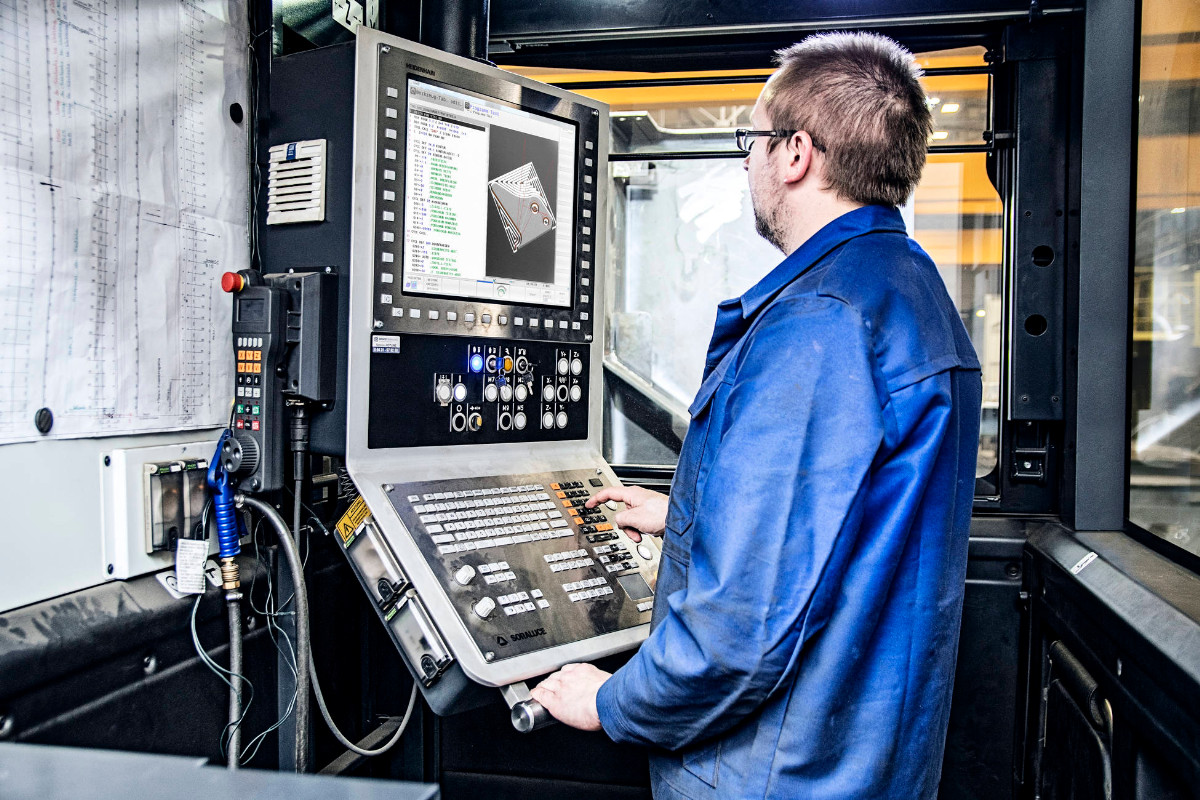
NC- und CNC-Daten für die zu fertigenden Bauteile liegen im Netzwerk, an das die verschiedenen Maschinen angeschlossen sind. Bearbeitungsmaschinen wie Fräswerk oder Drückportal werden so direkt mit den notwendigen Daten versorgt.
„Im Meisterbereich schauen wir uns die 3D-Modelle auch direkt am Rechner an. So können wir genau analysieren: Wie fertigt man am günstigen? Welche Vorgehensweise ist effizient? Welche Reihenfolge im Zusammenbau ist sinnvoll? Wir versuchen, das Datenmodell so genau wie möglich umzusetzen. Dazu müssen wir die Physik des Bauteils verstehen und beherrschen. So einfach wie in der Theorie ist es in der Praxis ja meistens nicht. Die digitale Technik unterstützt uns zum Beispiel darin, verschiedene Zustände zu simulieren, zwischen Ausgangszustand und Endzustand zu unterscheiden.“ (Olaf Jasinski, Meister Zusammenbau)
Das Ziel beim Einsatz digitaler Modelle ist klar: das Zusammenwirken von Schlosser, Schweißer und beispielsweise CNC-Fräser soll effektiver und präziser vonstatten gehen. Die Geschwindigkeit von Schweißportal oder Fräswerk hat sich in den letzten Jahren vervielfacht – auch weil manuelle Steuerungen durch Automatisierung abgelöst wurden. Die Genauigkeit einer CNC-Fräse ist im manuellen Betrieb selbst für erfahrene Kollegen nur schwer zu erreichen – die Schnelligkeit hingegen ist konkurrenzlos.
„Manchmal programmiert man länger als die Maschine dann für die Ausführung benötigt,“ beschreibt Christian Graef, der bei PST sowohl konventionelle Fräsen als auch CNC-Fräsen bedient hat. „Man stellt sich das ja immer so vor: Man hat ein Programm, dann drückt man einen Knopf und dann geht das alles von allein. Das ist aber falsch. Wir programmieren zu 95 % selbst – aus der Zeichnung heraus oder auf Basis digitaler Daten. Die beste digitale Technik nützt nichts ohne das notwendige Fachwissen.“
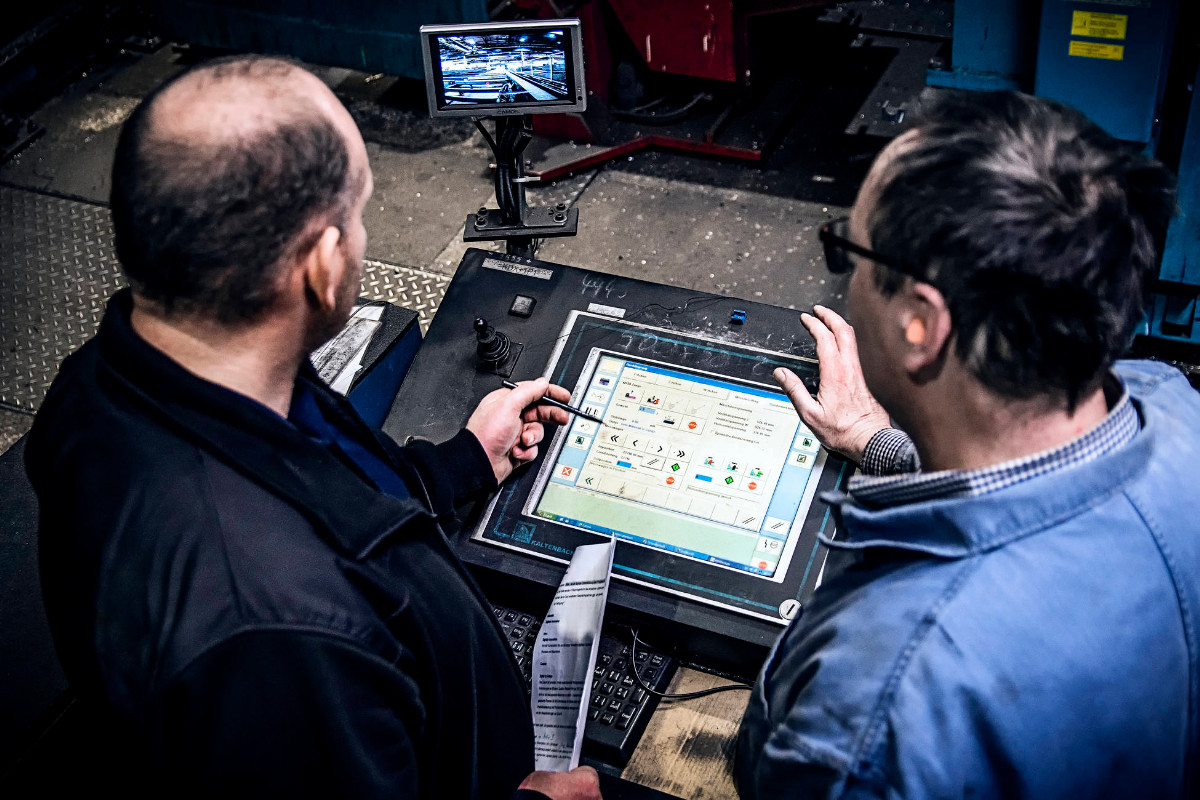
Digitale Technik braucht gut ausgebildete Mitarbeiter – das zeigt sich nirgends so deutlich wie in der Fertigung.
„Dir bringt die schönste digitale Werkstatt nichts, wenn du keinen hast, der mit den Maschinen klarkommt. Wenn man eine konventionelle Maschine ordentlich bedienen kann, hat man mit digitaler Steuerung kein Problem.“ (Christian Graef)
Die Vermessung
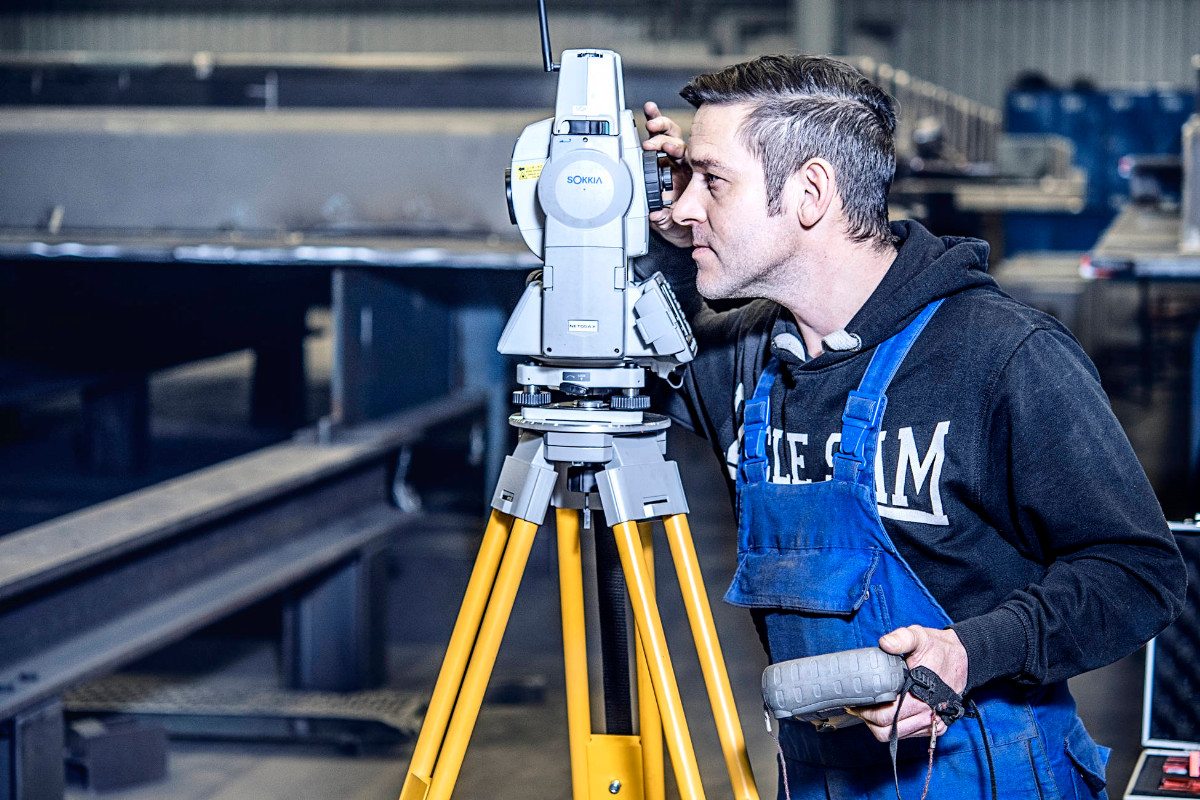
Während aller Bearbeitungsschritte erfolgt bei PST ein Abgleich zwischen Datenmodell und physischem Werkstück. Wir stellen an jeden Bearbeitungsschritt neben der Einhaltung der Terminsicherheit höchste Ansprüche in Sachen Präzision und Qualität.
Dazu kommen Hochpräzisions-Geräte zum Einsatz wie ein Tachymeter modernster Herstellung. Anhand des Modells wurden schon in der Arbeitsvorbereitung gemeinsam mit allen Ausführenden Messpunkte vereinbart, die im gesamten Projektverlauf als Referenzpunkte dienen. Auf dieser Basis können definierte Soll-Koordinaten jederzeit mit den realen Ist-Koordinaten abgeglichen werden, um Abweichungen und Verschiebungen festzustellen.
Das schon mit dem Modell angelegte Vermessungsprotokoll dokumentiert so den gesamten Produktionsprozess und ist ein wichtiges Dokument für die Qualitätssicherung.
„Die begleitende Vermessung fängt schon im Zusammenbau an. Wenn die Einzelelemente zusammengebaut werden, muss sichergestellt werden, dass bezogen auf die Einzelelemente die Geometrie stimmt. Daher fließen die Vermessungsergebnisse kontinuierlich in den Produktionsprozess ein. Fertige Bauteile vermessen wir dann, um deren Koordinaten mit den Baustellenkoordinaten abzugleichen. Ähnlich wie im Schiffbau. Ich klinke mich in das Bauteil über fest definierte Messpunkte ein und sehe sofort, ob ich in Höhe, Breite oder Tiefe Abweichungen habe.“ (Markus Ritter)
„Wir vermessen Einzelsegmente auf den Millimeter genau. Das geht nur mit digitalen Geräten.“
(Markus Ritter, Vermessung)
Digital by Design – Innovation digital gesteuert
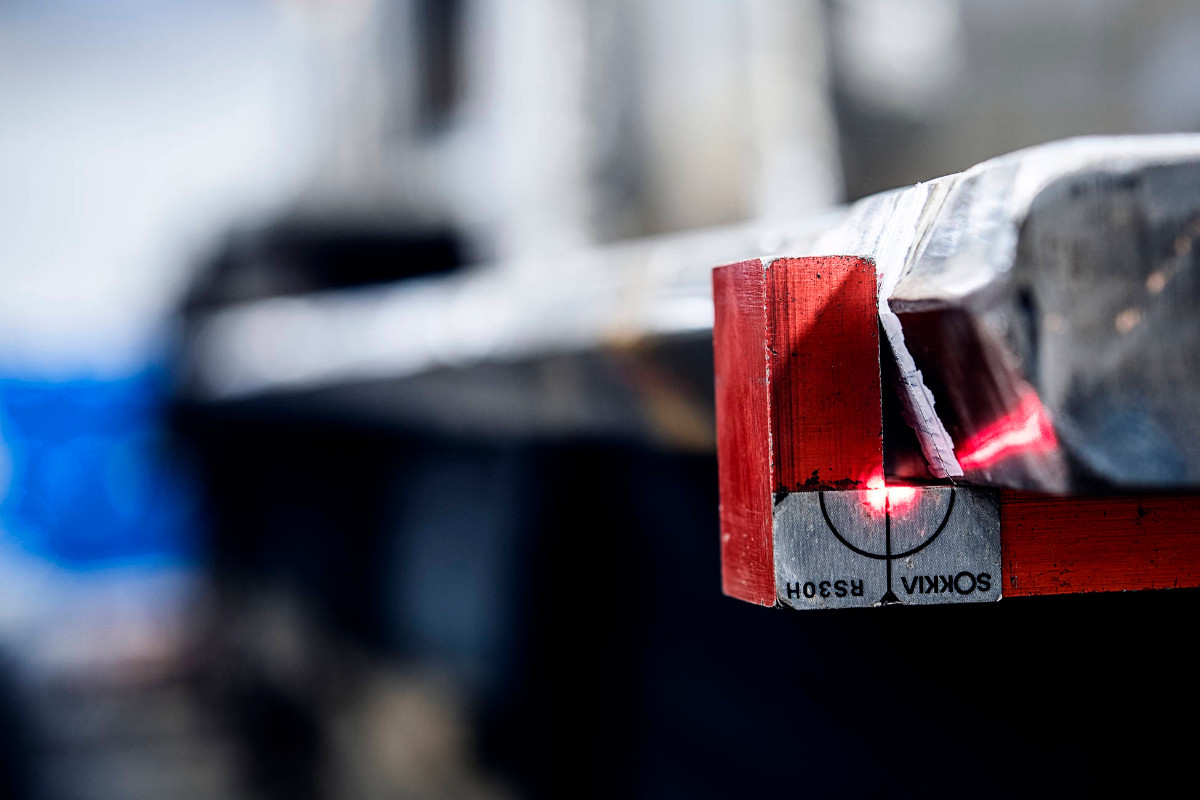
Bei PST simulieren wir schon weit vor der Montage den Endzustand auf der Baustelle. Somit können wir vorausschauend produzieren und jederzeit effektiv auf auftretende Abweichungen reagieren. Im Rahmen der Qualitätssicherung arbeiten wir in jedem Produktionsschritt mit innovativen digitalen Technologien – von der Arbeitsvorbereitung bis zur Konservierung. Ob interne Objektverwaltung, Instandhaltung oder Controlling: die Basis unserer Arbeit sind immer häufiger digitale Daten, die effiziente Prozesse und innovative Methoden ermöglichen.
Die Zukunft mit ihren komplexen Herausforderungen tickt digital. Deshalb arbeiten wir heute schon mit den Möglichkeiten der Zukunft.
Digital gesteuerte Innovation: Plauen Stahl Technologie ist „digital by design“.